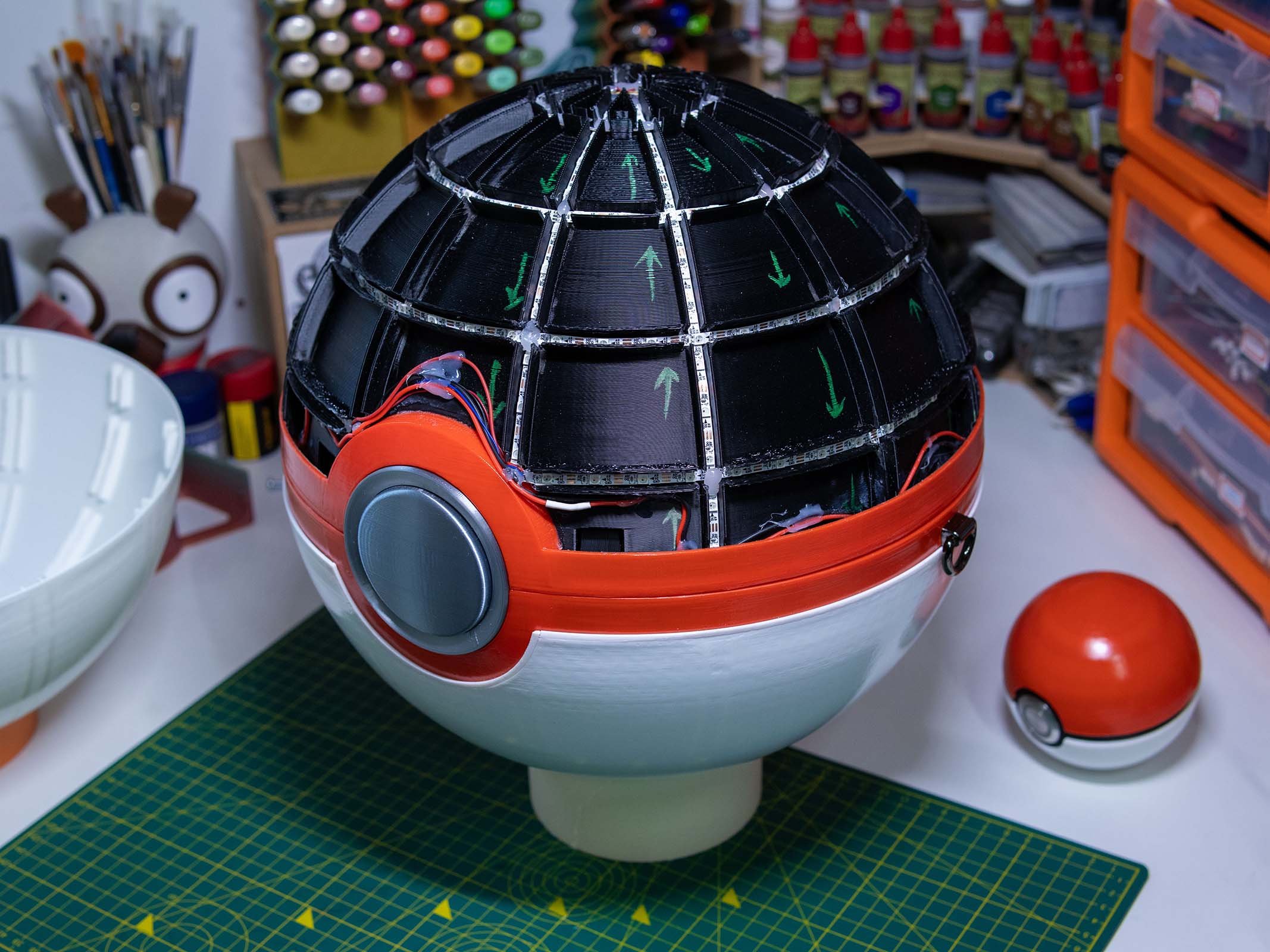
DYNAMAX BALL
I don’t typically give cosplay props their own page, but the Dynamax Ball is different.
Props absolutely require a great deal of work and effort, but often don’t contain as much original design or feats of engineering. This prop was an exception to this, requiring me to completely redesign common visuals (the Pokeball) to accommodate all the requirements I had in mind. I had to reassess my tools and push them to their limits. I had to solve for interesting and challenging design problems to get the end result I desired.
In the end, the Dynamax Ball took well over a year to accomplish. But it was completely worth it.
I typically make an effort to document my projects within an inch of their life, and to later share said projects open source so others could make their own explorations with it. This one, sadly, did not go entirely to plan and as a result things both didn’t get documented as thoroughly as I would have liked, nor did design files ever reach a place where I felt comfortable sharing them.
As an unintended result of this, this Dynamax Ball is the only one of it’s kind. But I still want to share what I can about it so others can both learn from and appreciate the work that went into it.
To that end, I will go into considerably more detail here than I usually do on my projects. If you want to know all the juicy little tidbits that went into this build, read on! And don’t forget to check out Klara’s page as well!
I love the idea of taking a fantastical, fictional item and making it real. The more far out the object, the more interesting it is to puzzle out how to bring it into reality.
The Dynamax Ball provided some interesting design challenges to solve for. The way the lights shimmered and moved over the sphere shining only through grid like openings was key to pulling off the prop. I also needed to design the build explicitly for the tools I had available; primarily 3D printers and commercially available hardware.
I also quickly realised that as a prop intended to be carried around while wearing my Klara costume, I would be suffering quite quickly if I just had a giant plastic ball to carry around at all times.
Thus hatched the idea of giving the Dynamax Ball dual purpose; it would serve as an awesome, life size rendition of the essential game item, and double as a fully functional handbag.
Of course, this also meant needing to design 3D printable hinges, latches, and opening mechanisms as well. I was definitely in for a wild ride.
The Dynamax Ball needed one more extra bit of pizazz to really make it special. The ability to turn the lights on and off from a distance felt like the secret sauce, and I knew just where to put that secret on/off switch; inside a regular Poké Ball.
In addition to the Dynamax Ball, I designed this palm sized, traditional Poké Ball that worked in a non-traditional way. Most pre-existing 3D printable Poké Balls feature the ability to open up and have an open space inside. I designed mine with twist lock shells for easy access, as the beautiful metal button doesn’t open up the ball itself but instead triggers the electronics stored inside. And that’s what makes the magic happen.
Inside the Poké Ball is a 5000 mAh lithium ion battery, connected to a power management board which both powers the QT Py C3 ESP-32 board and allows for charging of external devices. It also powers the metal momentary switch that triggers the code that talks to the Dynamax Ball.
The actual Dynamax Ball came together in pieces.
I designed it to be printed in pieces, partly to utilise printing in the colour I needed it to be, and partly because the whole thing was going to be so large it would only fit on my largest 3D printer in pieces. The whole thing is a whopping 30 cm in diameter, which fills the whole print bed of my Creality CR-10S Pro V2.
The design consists of a few main components. The black inner walls of the ball also serve as the housing for the LED strips, as well as the physical button latching mechanism. The outer white layers act as diffusion for the LEDs and are a mere 2 mm in thickness to allow for optimal light penetration. The red rims bring the black and white layers together, and also hide the springs required to open the ball. A metal invisible hinge sits embedded at the back allowing the whole thing to swing open, providing access to the inner chamber to store items.
The LEDs are of course the quiet star of the show beneath the surface of it all. When the lights are off, there are no sign of them (a clever trick I was pleased to pull off) but when the switch is flipped, the real fun begins.
I used strips of WS2812s, otherwise known as Neopixels, that were a mere 4 mm wide and featured 60 LEDs per metre of strip. The solder pads were small, exceptionally small, only 1 mm across and sat right next to two other tiny pads. I did the math to try and estimate how many metres I might need to fill every track on the sphere.
Estimations told me to prepare 10 whole metres of LEDs. I was in for a lot of soldering.
I arranged the strips in a serpentine fashion, starting at the bottom of the ball where the power and data would feed through a hole on the bottom. I drew arrows on the 3D printed part to help me visualise the direction of the data, as I knew it would be far too easy to get turned around with it. The strips went back and forth, then around the circumference. Wires connected the top and bottom hemispheres, where the process began all over again.
Of course, addressable LEDs with no microcontroller or power are not particularly exciting and don’t do a whole lot.
And I had a LOT of LEDs to deal with. 535 to be exact.
That would require a hefty amount of power and a chunky microcontroller to drive it all. And of course, it would need a place to put it all.
Most electronics projects have an internal space that can be used for storing all the boards and wires and batteries, and since this project required having a clean, open, internal space, I had to get creative with where the electronics would go. I designed a twist lock panel for the bottom of the ball to hide the electronics while also allowing access when need be.
The panel itself has the battery board screwed onto the other side, where the four 3000mAh 18650 Lithium Ion batteries live that power the arsenal of LEDs that snake around the ball’s inner layer.
Even though it only takes up a tiny amount of space at the very bottom of the Dynamax Ball, the PixelBlaze microcontroller is not just the brain of the electronics, but the heart of the very project itself.
Everything about the PixelBlaze is magnificent.
From its form factor to its built in ESP-32 chip (enabling Wi-Fi, for those of you not already familiar) or its wonderful community propping up an active animation library that anyone with a PixelBlaze can use, it truly is the Cadillac of microcontrollers for all kinds of LED projects.
I massively benefitted from the community with the project, as they often came to the rescue with questions about specifics (like whether or not I could attach an RF receiver to it) and provided me with an awesome selection of animations to choose from. The animations are basically the one part of the Dynamax Ball I did not do myself.
The PixelBlaze also greatly improved the experience of mapping the LEDs to enable the incredible fully three dimensional animations that race across its surface. There are no hidden seams or slight of hand here; just honest to god 3D mapping of 535 LEDs.
Last, but certainly not least, is the latching mechanism for the Dynamax Ball itself.
When I decided to turn prop into usable object, I knew I was tacking on a great deal of extra engineering, especially given the constrains of the materials I had chosen to use. While I could access some machined parts (like compression springs and thick gauge wire), I was largely restricted to electronics and 3D printed pieces to design a way for the hemisphere to both stay closed when I needed and open on command with the push of a button.
While many ideas were toyed with, including that of an electromagnetic latch, I ultimately settled on a solution that is purely mechanical.
The entire system is carefully tensioned between 9 compression springs, ranging across 4 different amounts of force. Because these springs both need to be able to force upwards close to one kilogram of plastic and electronics, and press tight the two latches that fight against that upwards force, the balance between everything had to be just right or everything would fail.
Utilising small 3D printed levers, I was able to create a path from the big silver button in the front, through a peg that can move through the button base, to the T shaped lever hidden inside an enclosure, which exerts pressure on the bottom of the latches to force the tops back against the springs. This releases the top hemisphere, and the two springs hidden in the red rim can do their job of bouncing the whole thing up.
It is a surprising deal of effort to simply make a hard shell bag open and close.
As you can now perhaps appreciate a bit better, there’s a lot going on under the hood here.
But of course, all everyone REALLY wants to know is how I got the outside so dang shiny.
While I would be lying to say there wasn’t SOME good old fashioned elbow grease involved (especially for the huge external hemispheres), the secret ingredient to how I got both the Poké Ball and Dynamax Ball looking so smooth and shiny is in the 3D printing material used.
Everything externally facing on both pieces was printed in Polymaker PolySmooth, otherwise known as PVB.
PVB is exciting because it combines the easy printing of PLA with the vapour smoothing abilities of ABS, only with isopropyl alcohol instead of acetone. I was able to use my Polysher to make the Poké Ball a breeze, but the Dynamax Ball required polishing by hand, which is considerably more time consuming.
Worth it though? I would say absolutely yes.